Product Introduction
Strengthening airflow dryer is a transmission device equipped with a dispersed material at the bottom of the drying pipe to break the filter cake material, increase the heat transfer area of the hot air and the material, and strengthen the drying process. At the same time, the high-speed rotating dispersing device generates a high-speed turbulent airflow, so that the material and the hot air always maintain a relatively high relative speed, and also plays a role of strengthening the drying.
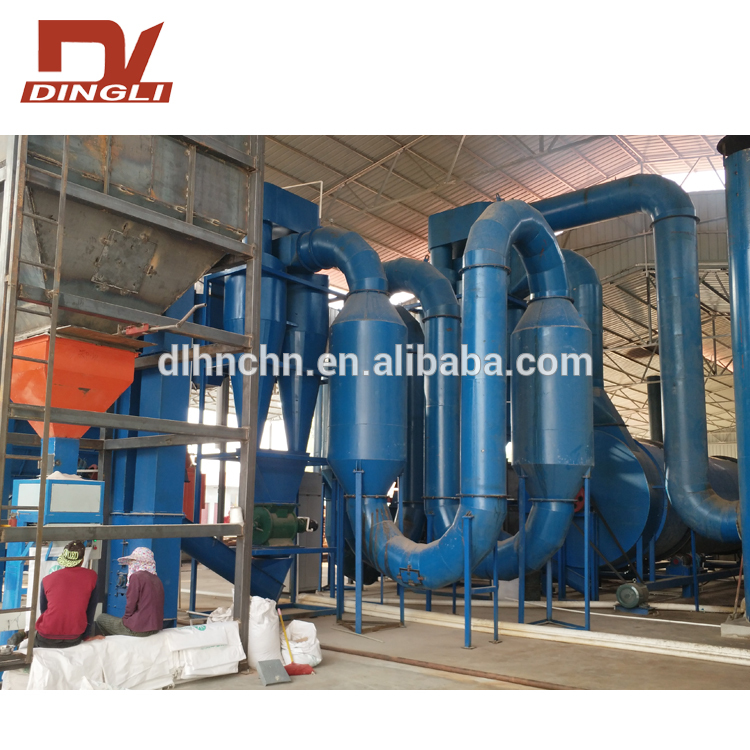
Product Features
1. The drying time is short and the dehydration speed is fast, generally 0.5-3 seconds. The thermal efficiency is high and the product does not overheat. High degree of automation and good quality of dry products.
2. It has high drying strength and dewatering capacity from 25 kgH2O/h to 2000 kgH2O/h.
3. The equipment is simple, the floor space is small, and the investment is saved. The GQW type is a special low-height compact type.
4. Wide range of applications, can be applied to a variety of powder particles, paste, filter cake materials.
5. According to the user's situation and the heat resistance temperature of the material, steam, electricity, hot blast stove, flue gas furnace, boiler flue gas waste heat, etc. can be selected as the heat source. The temperature of the heat medium can be selected from 120 ° C to 780 ° C.
Type A: Suitable for non-sticky, loose materials
Suitable for non-sticky, loose materials, finished products are dry for granules and powder materials. The dryer is widely used in food, chemical, pharmaceutical, building materials, feed and other industries. Such as: wood chips, wood flour, wood powder, rice husk, rice bran, bran, tea residue, resin, starch, glucose, fish meal, sugar, sugar, distiller's grains, feed, gluten, plastic resin, mineral powder, coal powder, dyes, etc.

Type B: Suitable for paste-like and filter cake materials
Suitable for the drying of paste-like and filter cake materials with relatively large moisture content. Such as: distiller's residue, corn protein, sludge residue, peat, clay, clay cement, kaolin, bone meal, diatomite, gypsum slurry, lime, bentonite, acrylamide, ABS resin, synthetic resin, white carbon black , phenylchapyrazolone, catechu, oxalic acid catalyst, accelerator, catalyst, precipitated carbon powder, p-aminosalicylic acid, calcium hydrogen phosphate, samarium, terephthalic acid, diethylammonium, titanium dioxide, activity Carbon, sodium fluorosilicate, fluorite ore, by-product ammonium sulfate, silica gel powder, calcium sulfonate, polypropylene resin, chlortetracycline, chlorinated coffee grounds, oral glucose, sodium sulfate, phosphate rock, tetracycline, three Iron oxide, calcium carbonate, potato flour, tail coal, stearate, pharmaceuticals, pharmaceuticals, iron oxide, etc.
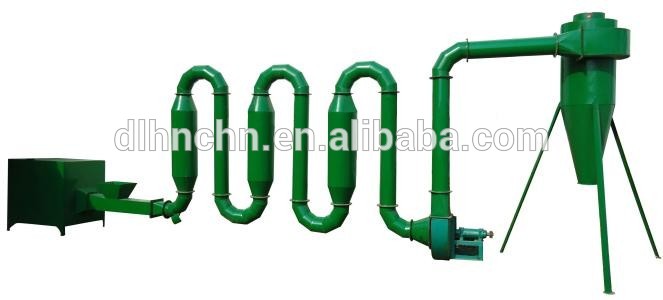
Working Principle
The wet material is continuously fed into the dryer through the quantitative feeder. During the falling process, it meets with the hot air heated by the heat source, and part of the water evaporates, so that the viscosity of the material is lowered, falls to the pulverizing device, and is pulverized into powder by the pulverizing device. materials. The powdery wet material is suspended in hot air, the material is continuously tumbling, the heat transfer area is increased, and the heat transfer coefficient is improved. The dried powdery product is separated into the cyclone with the gas flow, and the exhaust gas is filtered through a bag filter and then emptied.
Model | Evaporation Capacity(kg/h) | Air Volume(kg/h) | Inlet Air Temperature(℃) | Installed Power(KW) | Area(㎡) |
DLAP200 | 65-350 | 2500-2800 | 140-600 | 23 | 16 |
DLAP250 | 100-750 | 3800-4400 | 140-600 | 29 | 20 |
DLAP350 | 190-1200 | 7600-8600 | 140-600 | 42 | 32 |
DLAP450 | 360-1700 | 9900-11300 | 140-600 | 67 | 40 |
DLAP600 | 520-2300 | 22000-25000 | 140-600 | 116 | 55 |
Except above models, we also can supply special model according to your requirements. |