The three cylinder dryer is mainly used for granularity material which is in the range of a certain humidity,such as yellow sand which used in dry mortar industry,all kinds of casting sand in casting industry,slag in building materials industry;also can drying small granularity clay,coal,coal ash,iron powder,ore,silica sand and so on.
Advantages
1.Compact structure,small floor area,the length cut down 60% than single cylinder rotary dryer,be helpful to plant layout;
2.High technical content, self heat preservation, thermal efficiency more than 80%(single cylinder dryer only 35%),fuel(coal) saving 68%,capacity increased 50%;
3.Reliable working condition,low consumption,high heating efficiency,good drying effect for materials,more automatic,less operate workers;
4.High temperature wear easy deformation parts adopt to durable wear resistant alloy steel,wearing-resisting 4times than common steel,long lifetime,easy maintainance;
5.Outlet temperature less than 60 degree,can continuous production and or packing;
6.Civil engineering investment lower about 50%,electric reduce about 60%;
7.Need not drive by gear,adopt to supporting roller for rotating;
8.The final humidity can adjust as customer's demands,the final humidity can less than 0.5%;
9.It is drying for less than 20mm pieces,granularity,powder materials. three return dryers
Working principle
1.The material first goes into the inside drum, because there are the spiral shape boards fixed in the drum, when the dryer make rotary working, the spiral shape board will stir the material and make the material do movement. three return dryers
2.When the material reaches the right side of the drum, it will go into the second drum for further drying.
3.The same working principle, the material then goes into outside drum, during the drying working process, thematerial will make three times drying, so the material can be dried completely in this process.
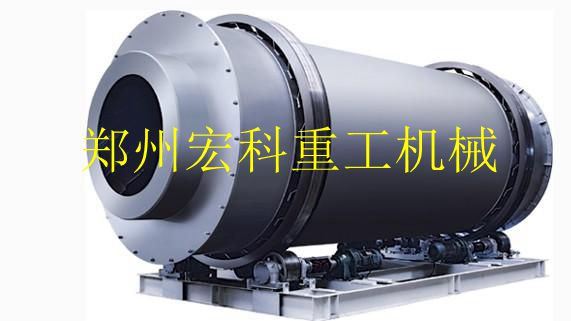
Ball Mill Technical Data:
Specification | φ 2.0× 6m | φ 2.5× 6.5m | φ 2.7× 7m | φ 3× 7m | φ 3.2× 7m | φ 3.6× 8m | φ 4.2× 8.5m | |
Diameter(m) | 2.0 | 2.5 | 2.7 | 3 | 3.2 | 3.6 | 4.2 | |
Length(m) | 6 | 6.5 | 7 | 7 | 7 | 8 | 8.5 | |
Shell volume (m3) | 18.84 | 31.89 | 40.5 | 49.46 | 56.26 | 81.38 | 118 | |
Shell rotary speed(rpm) | 3-10 | 3-10 | 3-10 | 3-10 | 3-10 | 3-10 | 3-10 | |
Material stay time (min) | 12-30 | 12-30 | 12-30 | 12-30 | 12-30 | 12-30 | 12-30 | |
Material moisture (%) | 6-25 | 6-25 | 6-25 | 6-25 | 6-25 | 6-25 | 6-25 | |
Mafter moisture after drying(%) | ≤ 1 | ≤ 1 | ≤ 1 | ≤ 1 | ≤ 1 | ≤ 1 | ≤ 1 | |
Max inlet temperature | 750-900 | 750-900 | 750-900 | 750-900 | 750-900 | 750-900 | 750-900 | |
Production capacity (T/H) | Ore slag | 20-25 | 25-30 | 30-35 | 35-10 | 40-45 | 50-65 | 70-85 |
Flyash | 10-17 | 17-21 | 20-25 | 23-27 | 25-30 | 30-45 | 45-63 | |
Sand | 20-27 | 25-40 | 27-45 | 30-45 | 35-50 | 55-75 | 75-99 | |
Motor model | Yr160m-4 | Yr132m-4E | Yr160m-4 | Yr160m-4 | Yr132m-5E | Yr160m-4E | Yr160m-4E | |
Motor power (kw) | 7.5× 2 | 11× 2 | 7.5× 4 | 7.5× 4 | 11× 4 | 15× 4 | 18.5× 4 | |
Speed reducer model | XWD-6 | XWD-6 | XWD-6 | XWD-6 | XWD-6 | XWD-8 | XWD-8 | |
Speed ratio(I) | 17-29 | 17-29 | 17-29 | 17-29 | 17-29 | 17-29 | 17-29 | |
Weight (T) | 25 | 32 | 35 | 38 | 43 | 57 | 77 |