2013 stainless steel rotary drum dryer
1.Introduction of stainless steel rotary drum dryer
Industrial drying equipment is mainly used in building materials manufacturing, metallurgy and chemical industry, and cement pr 2013 stainless steel rotary drum dryer oduction industry, etc. to dry mineral slag, limestone, coal powder and clay, etc.
If used in combination with our coal gasifier, our dryer can also be used for fine chemical drying.
Our industrial dryers are also regularly used in compound fertilizer production lines.
2.Main features of stainless steel rotary drum dryer
1). Our dryer is designed with anti-sticky drum-wall and assembled material-lifting board.
2). This drying equipment is divided into secondary-granulating section, balling section, polishing section and drying section, etc. What worth mentioning is that our dryer features convenient installation and transportation as a result of its flange connection.
3). Our dryer has the features of low noise, little pollution and good drying effect.
3.The working principles of stainless steel rotary drum dryer
I produced a rotary kiln system and equipment through technology innovation, the system used in the most advanced hydraulic gear wheel device, adopts the high precision measurement of piston pump, high precision control valve and contact graphite block seals and other advanced technologies.
- To improve the degree of automation, an industry watch TV Kiln fire, process simulation screen, burning zone by infrared scanning apparatus to Duanshao calcined with a direct reflection of the computers.
- Thermal stability of the system, improved equipment operation rate, compared with the same specifications of equipment, operating rate of 10%, yield 5% -10%, 15% lower heat consumption.
4. Stainless steel rotary drum dryer tecnical parameters:
item(m) | priductive capacity(t/h) | revolution(r/min) | motor power(Kw) | install angle(.) | Temp.of final |
Φ1.0×5.0 | 0.5-1.2 | 0.6-6 | 4 | 3-5 | ≤1.5% |
Φ1.2×6-10 | 1.5-3 | 0.6-6 | 5.5 | 3-5 | ≤1.5% |
Φ1.5×12-18 | 3-5.5 | 0.6-6 | 15 | 3-5 | ≤1.5% |
Φ1.8×12-18 | 5-6.5 | 0.6-6 | 18.5 | 3-5 | ≤1.5% |
Φ2.2×12-22 | 7-12 | 0.6-6 | 22 | 3-5 | ≤1.5% |
Φ2.4×15-20 | 9-15 | 0.6-6 | 30 | 3-5 | ≤1.5% |
Φ3.0×25 | 16 | 0.6-6 | 55 | 3-5 | ≤1.5% |
model | heat direct and sequence | heat direct and retrograde | compound heating | |||
type of material | mineral | HP | ammonium sulphate | phosphorus fertilizer | coal | |
capacity kg/h | 1000 | -66 | 15000 | 20000 | 12000 | 5000 |
primary moisture % | 30 | 13 | 6 | 1.5 | 5 | 6.5 |
final moisture % | 15 | 0.3 | 1 | 0.1 | 0.1 | 0.1 |
average dim. mm | 6.5 | 0.05 | 4.7 | 0.5-0.7 | 0.5 | 5 |
thickness of material mm | 770 | 800 | 1890 | 1100 | 1500 | 750 |
capacity of hot air kg/h | 39000 | 5400 | 10750 | 9800 | 6500 | 16000 |
temp. of air in | 600 | 165 | 500 | 180 | 650 | 570 |
temp. of material out | 42 | 100 | 70 | 80 | 75 | |
heating style | gas | steam electric+heating | heavy oil | coal fuel furnace | heavy oil | heavy oil |
ratio of feed | 6.3 | 7 | 7.5 | 7.8 | 18 | |
rotation speed rpm | 4 | 4 | 3.5 | 3 | 4 | 2 |
angel . | 0.04 | 0.005 | 0.03 | 0.05 | 0.05 | 0.043 |
quatity of oar | 12 | 24 | 12 | 22 | 8 16 | 6 12 |
dim. of drier m | 2.0 | 1.5 | 2 | 2.3 | 2 0.84 | 24 0.95 |
length of drier m | 20 | 12 | 17 | 15 | 10 | 16 |
driving power kw | 22 | 7.5 | 15 | 11 | 11 | 15 |
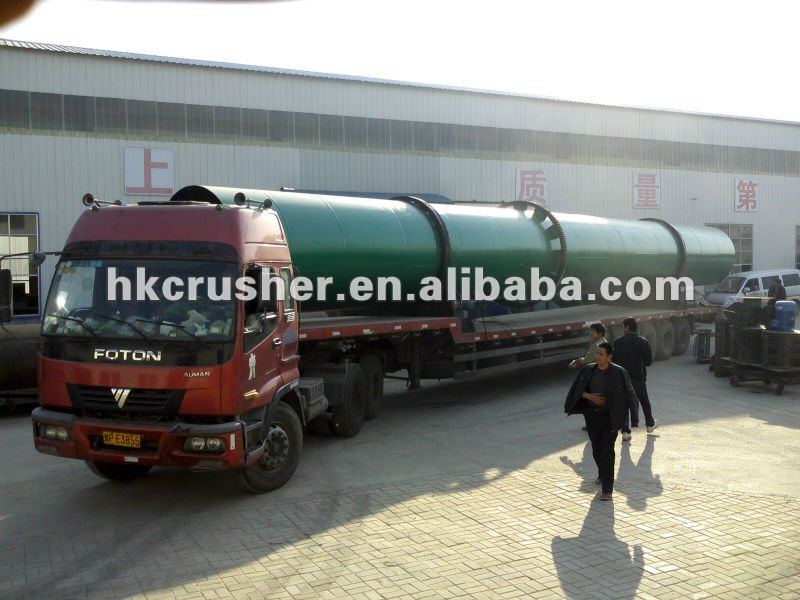
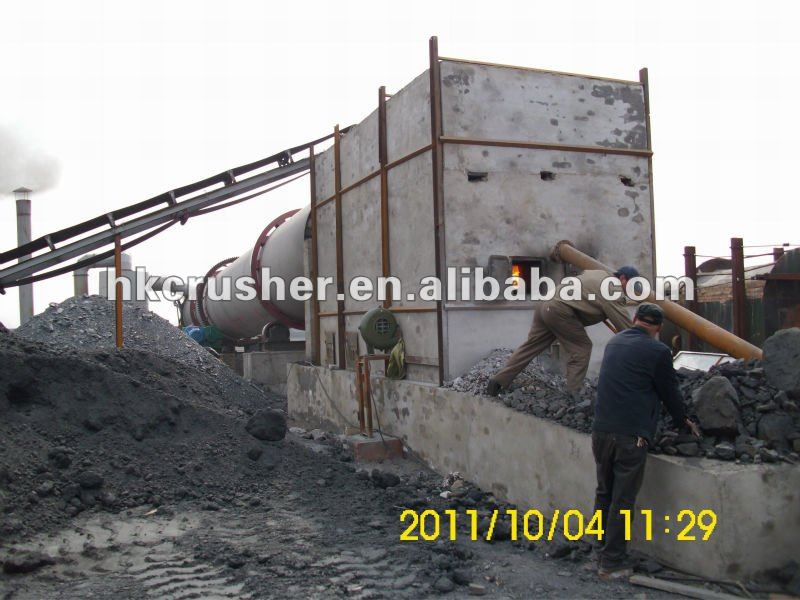
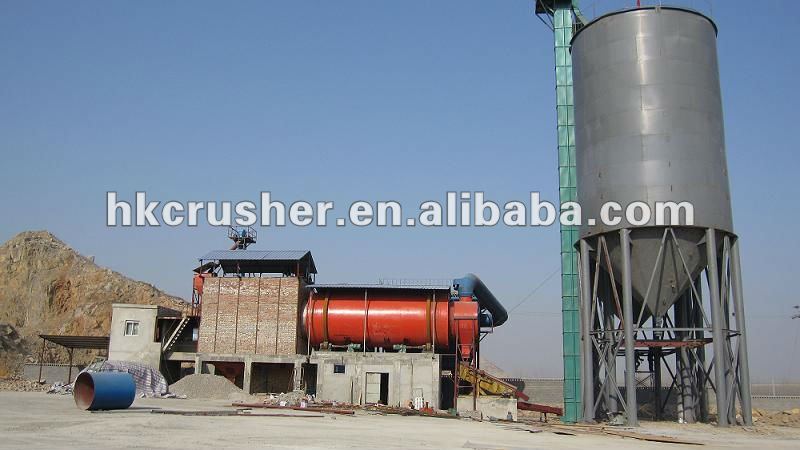