DESCRIPTION
Wet material is loaded from one head of the dryer, and then it is stirred by the bafflers that is uniformly distributed in the barrel. Material is uniformly distributed and dispersed in the dryer, fully contact the hot air of parallel (or counter) flow, so the drying process is expedited, and the impulsion power of media transfer is enhanced. During the drying process, material is under the effect of angled baffler and hot air, moves to the star shape unloader that is at the other head of the dryer.
FEATURES
The motorization level of the barrel is high, and the production capacity is high;
The resistance that the material passes through the barrel is less, and the power consumption is low.
Application capability to different characters of materials is high.
The operation is stable, the operation fee is low, and the uniformity of product drying is good.
APPLICATIONS
Applicable for drying big particles, heavy particles in chemical, mining,and metallurgy, such as mining area, cinder of blast furnace, coal, powder of metal, phosphate fertilizer and thiamine. For drying the powder or particles with special requirements, such as HP foaming blowing agent, residule of alcohol, light calcium carbonate, active clay, magnetic powder, graphite, and residue of medicine. For materials to be dried under low temperature and large lot continuous production.
FEATURES
The motorization level of the barrel is high, and the production capacity is high;
The resistance that the material passes through the barrel is less, and the power consumption is low.
Application capability to different characters of materials is high.
The operation is stable, the operation fee is low, and the uniformity of product drying is good.
FLOW CHART
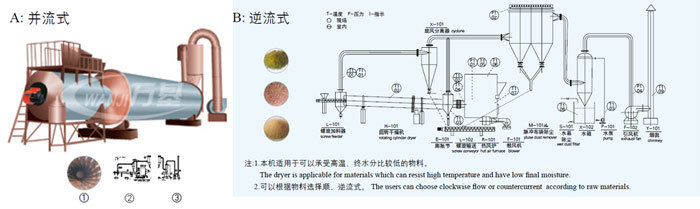
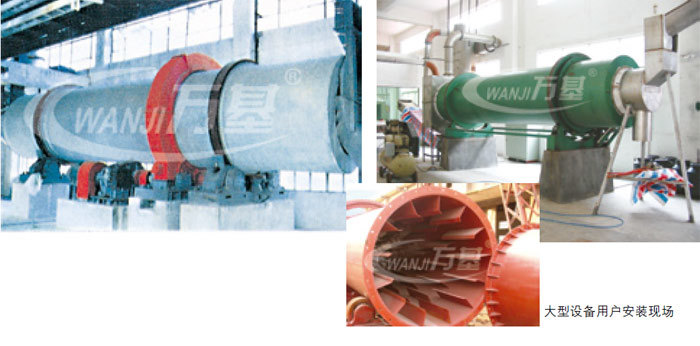
TECHNICAL PARAMETERS
item (m) | productive capacity (t/h) | revolution (r/min) | motor power (kw) | install angle (°) | Temp. of final |
ø1.0×5.0 | 0.5-1.2 | 0.6-6 | 4 | 3-5 | ≤1.5% |
ø1.2×6-10 | 1.5-3 | 0.6-6 | 5.5 | 3-5 | ≤1.5% |
ø1.5×12-18 | 3-5.5 | 0.6-6 | 15 | 3-5 | ≤1.5% |
ø1.8×12-18 | 5-6.5 | 0.6-6 | 18.5 | 3-5 | ≤1.5% |
ø2.2×12-22 | 7-12 | 0.6-6 | 22 | 3-5 | ≤1.5% |
ø2.4×15-20 | 9-15 | 0.6-6 | 30 | 3-5 | ≤1.5% |
ø3.0×25 | 16 | 0.6-6 | 55 | 3-5 | ≤1.5% |
form | direct heating clockwise flow | heat directly countercurrent spec | compound heating | |||
kinds of raw materials | ore | HP vesiccant | slag of blast fumace | ammonium sulfate | phosphorus fertilizer | coal |
amount to be treated kg/h | 1000 | 466 | 15000 | 20000 | 12000 | 5000 |
primary moisture % | 30 | 13 | 6 | 1.5 | 5 | 6.5 |
final moisture % | 15 | 0.3 | 1 | 0.1 | 0.1 | 0.1 |
average diameter mm | 6.5 | 0.05 | 4.7 | 0.5-1.7 | 0.5 | 5 |
bulk density of raw material kg/m2 | 770 | 800 | 1890 | 1100 | 1500 | 750 |
amount of hot air kg/h | 39000 | 5400 | 10750 | 9800 | 6500 | 16000 |
temperature of air at inlet ºC | 600 | 165 | 500 | 180 | 650 | 570 |
temperature of raw material at outlet ºC |
| 42 | 100 | 70 | 80 | 75 |
way of heating | gas | electric heating | heavy oil | coal fuel hot fumace | heavy oil | heavy oil |
loading efficiency |
| 6.3 | 7 | 7.5 | 7.8 | 18 |
revolution rpm | 4 | 4 | 3.5 | 3 | 4 | 2 |
gradient m/m | 0.04 | 0.005 | 0.03 | 0.05 | 0.05 | 0.043 |
quantity of stirring-up rake | 12 | 24 | 12 | 22 | outer of inner cylinder 8 | outer of inner cylinder 6 |
diameter of dryer m | 2.0 | 1.5 | 2 | 2.3 | out cylinder 2 | out cylinder 2.4 |
length of dryer m | 20 | 12 | 17 | 15 | 10 | 16 |
driving power kw | 22 | 7.5 | 15 | 11 | 11 | 15 |