The spray drying is the technology widest used in the liquid technology shaping and in the drying industry. The drying technology is most suitable for producing the powder or particle solid products from the materials, such as: solution, emulsion, soliquoid and pumpable paste states. For this reason, when the particle size and distribution of the final products, their residual water contents, the stacking density and the particle shape must meet the precision standard, the spray drying is one of the most desired technologies.
PRINCIPLE
After the filtering and heating, the air enters into the air distributor on the top of the drier. The hot air enters into the drying room in the spiral form and uniformly. By passing through the high-speed centrifugal spray on the top of the tower, the material liquid will rotate and be sprayed into the extremely fine mist liquid beads. Through the very short time of contacting the heat air, the materials can be dried into the final products. The final products will be discharged continuously from the bottom of the drying tower and from the cyclone separator. The waste gas will be discharged from blower.
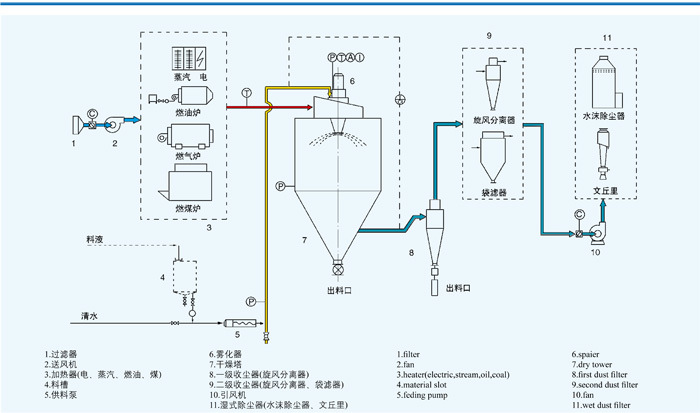
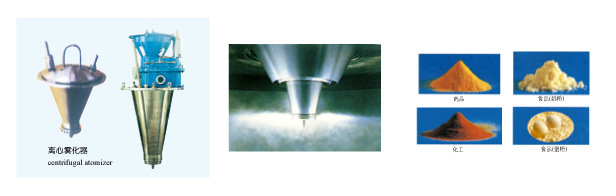
LPG-5 | LPG-10 | LPG-15 | LPG-20 | LPG-25 | LPG-50 | LPG-100 | LPG-150 | LPG-200 | LPG-500 | LPG-800 | LPG-1000 | LPG-2000 | LPG-3000 | LPG-4500 | LPG-6500 | |
Inlet temperature (ºC) | 140-350 automaticalty controlled | |||||||||||||||
Outlet temperature (ºC) | 80-90 | |||||||||||||||
Way of atomizing | High Speed centrifugal atomizer | |||||||||||||||
Water evaporation capacity (kg/h) | 5 | 10 | 15 | 20 | 25 | 50 | 100 | 150 | 200 | 500 | 800 | 1000 | 200 | 3000 | 4500 | 6500 |
Revolution of atomizer | 25000 | 24000 | 24000 | 22000 | 22000 | 21500 | 18000 | 16000 | 12000-13000 | 11000-12000 | ||||||
Diameter of atomizing tray (rpm) | 50 | 80 | 80 | 120 | 150 | 180-210 | Decided in accordance wiht the requirements of process | |||||||||
Max Electric heating power(kw) | 12 | 24 | 36 | 45 | 45 | 63 | 81 | 99 | ||||||||
Dried powder restoring rate(%) | ≥95 | |||||||||||||||
Length of convered area (m) | 1.6 | 2.7 | 3.0 | 3.5 | 4 | 4.5 | 5.2 | 7 | 7.5 | 12.5 | 13.5 | 14.5 | Decided in accordance the flow chart,condition of filed and requirements of customers. | |||
Width of convered area (m) | 1.1 | 1.5 | 1.8 | 2.0 | 2.7 | 2.8 | 3.5 | 5.5 | 6 | 8 | 12 | 14 | ||||
Heigth of tower body (m) | 1.75 | 3.0 | 3.5 | 4.0 | 4.5 | 5.5 | 6.7 | 7.2 | 8 | 10 | 11 | 15 | ||||
Hoisting heighr of nozzle(m) | - | - | - | - | 2.5 | 2.5 | 3.2 | 3.2 | 3.2 | 3.2 | 3.2 | 3.2 |
APPLICATIONS
Chemical Industry
Sodium fluoride (potassium), alkaline dyestuff and pigment, dyestuff intermediate, compound fertilizer, formic silicic acid, catalyst, sulphuric acid agent, amino acid, white carbon and so on.
Plastics and resin
AB, ABS emulsion, uric acid resin, phenolic aldehyde resin, urea -formaldehyde resin, formaldehyde resin, polythene, polychloroprene and etc.
Food Industry
Fatty milk powder, protein, cocoa milk powder, substitute milk powder, egg white (yolk), food and plant, oats, chicken juice,coffee, instant dissoluble tea, seasoning meat, protein, soybean,peanut protein, hydrolysate and so forth.Sugar, corn syrup, corn starch, glucose, pectin, malt sugar,sorbic acid potassium and etc.
Ceramic
aluminium oxide, ceramic tile material, magnesium oxide,talcum and so on.
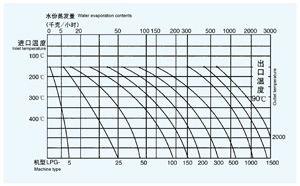
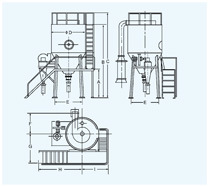
TECHNICAL PARAMETERS
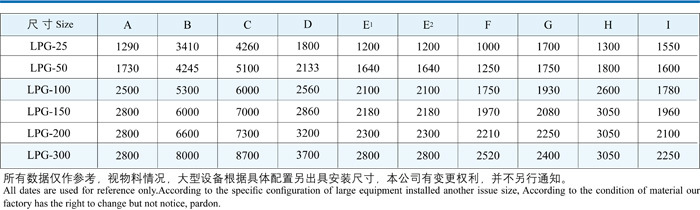