Machine Application:
1. Plastic recycling washing machine is applied in PET waste bottle or sheet recycling field.
2. Through crushing, washing and dry process, the waste bottle or sheet will become to be bottle flakes. The flakes are widely used in plastic industry, like sheet, and profile production.
3. The clean flakes can be used to produce the polyester staple fiber, PET strap band, granules, PET transparent film and sheets, etc. The top class flakes can be used to blow bottles again.
4. Recycling machine can be designed on the basis of how dirty the flakes are, and make sure of the quality of the final products are very clean.
5. Recycling machine output we can supply is from 300kg/h to 6000kg/h.
Machine Features:
PETBottle Washing and Recycling Line is the special equipment for breaking bottle and the waste plastic into the plastic granules. It can meet with both home and aborad requirements of recycling and reusing waste plastic.
Bottle Washing and Recycling Line output is 500- 6000kg/h . The shape of finidhed plastic granule material is less than 8mm.
Machine Technical Characteristics:
1.Final recycled PET flake quality standard:
Index | Parameter |
PET flake size | 8~12 mm |
Moisture | < 1.5 % |
Viscose | < 20 ppm |
PP/PE | < 20 ppm |
Metal | < 20 ppm |
Other color PET flake | < 30 ppm |
Label | < 20 ppm |
PVC | < 30 ppm |
Total impurities | < 100 ppm |
PH | neutral |
Bulk density | 0.3g/cm3 |
2. Estimated Plant Parameter:
Capacity(kg/h) | Installation Power(kw) | Required Area(m2) | Manpower |
500 | 220 | 600 | 8 |
1500 | 430 | 800 | 12 |
3000 | 650 | 1000 | 18 |
6000 | 1000 | 1400 | 30 |
Machine Process Flow Introduction:
Bottle bales→Bale Opening→Trommel Filtering→Label Removing→Bottle Pre-washing→Manual Sorting→Wet Crushing→Floating Washing→Drying→Hot Flotation Washer→Drying→Continuous Friction→Continuous Floating Washing→Drying→Label&Dust remover→Flake Optical Sorting→
Packing→Clean Flakes
Bottle bale opening
2. Belt conveyor
Put the material on the moving belt, which will convey the bottle into label remover
3. Trommel
Removing rock, stone, dust, loosen caps and small metals, especially, the iron will be removed by high speed
4. Bottle label separator
Removing labels from bottles
5. Manual Select working table
IF the label still in the bottle, worker can remove the label by hand
6. Belt conveyor
Put the material on the moving belt, which will convey the bottle into crusher
7. Crusher
Crush the material
8.Screw loader
Put the flakes into the Hot washer to clean
9. Floating washer
Cleaning flakes to remove chemicals and separating out rest labels and caps
10. Hot washer
Connected with steam boiler. Steam is supplied into washing tank to heat water and flakes. Hot water makes waste; label and glue loosen from bottles
11. Friction washer
After crushing material from enters the mouth, through the high speed on the axis of the blade flap and spray water to the common function of good cleaning effect
12. Centrifugal dryer
Rejection the water from the flakes, moisture content is less than 2%
13. Pipe drying system
Hot air drying
14. PVC (label) separator
Used for the PET bottles, round and pressed bottles,effective more than 98%,save energy and labor,without water
15. Storage bunker
Storage materials
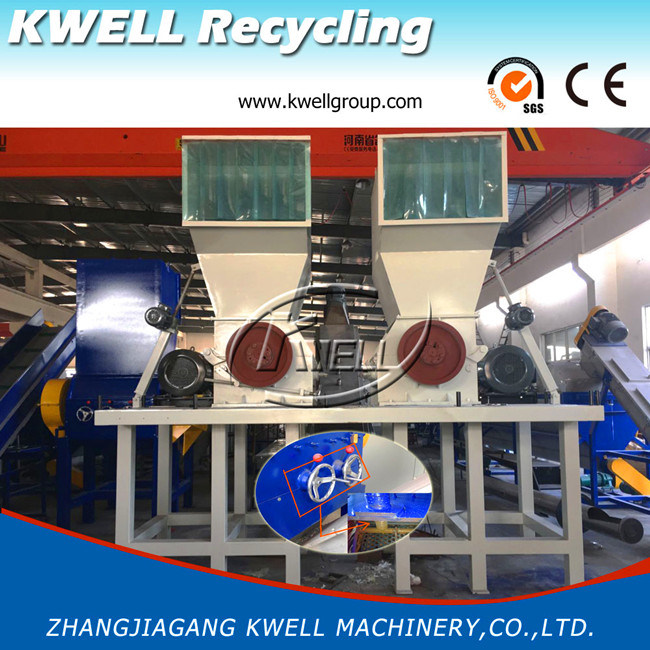
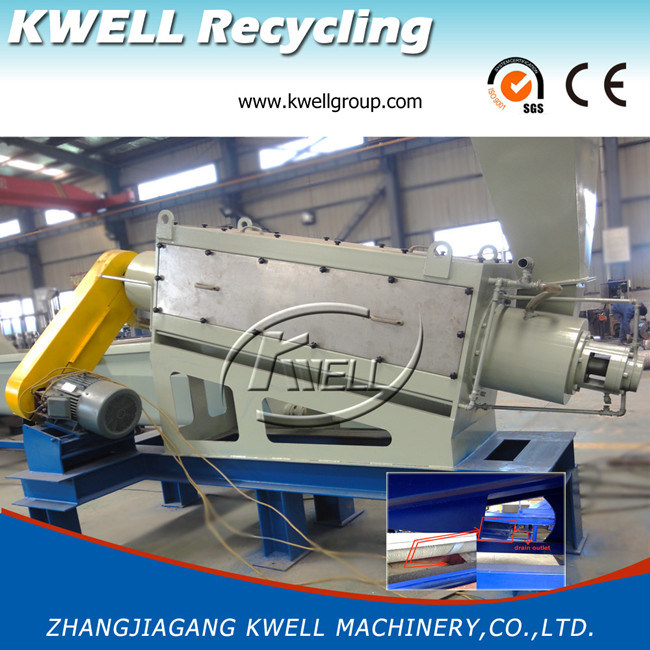
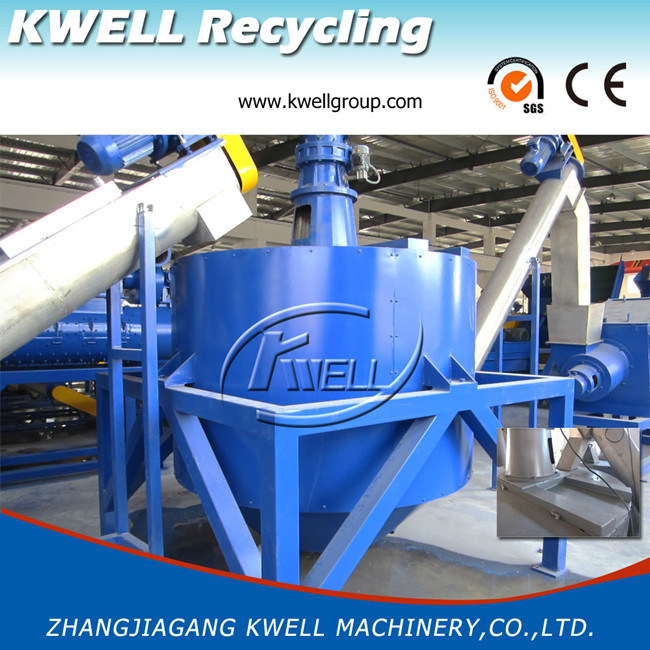
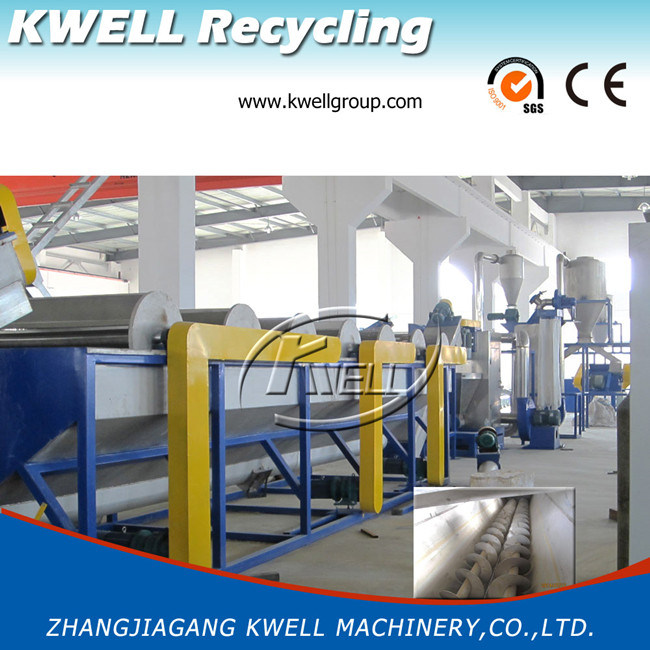
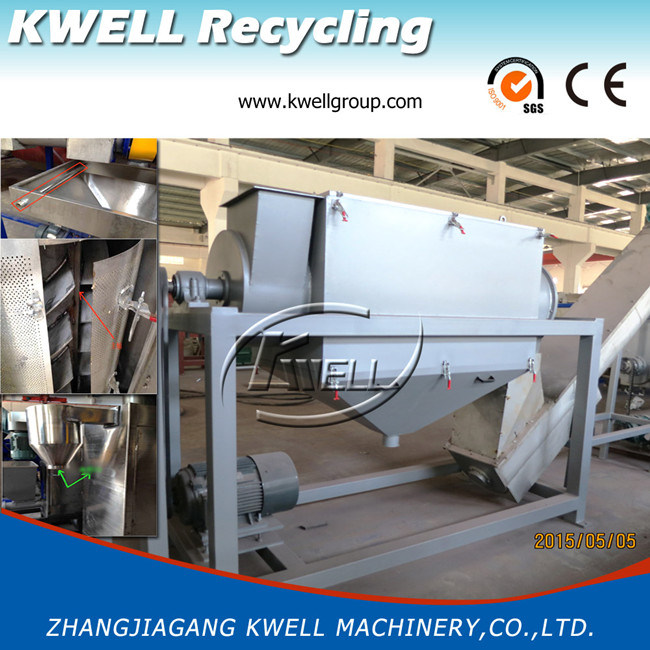
Machine Packing details:
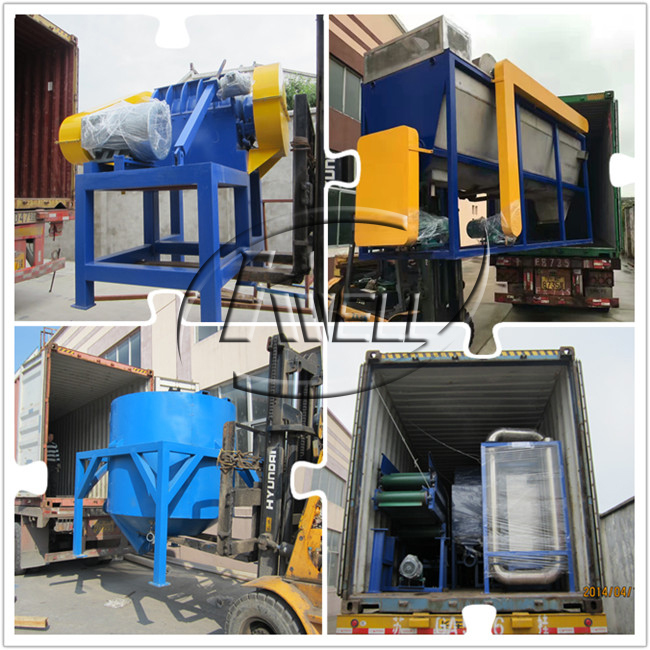
About our service:
PET Bottle washing line Before-sale
- Introduce products and applications detain
- Recommend suitable solution
- Provide with reference information
- Offer lab for test
- Provide with layout and engineering conditions
- Inform the project processing status
- Offer other documents
1. Provide with installation, commissioning and training
2. Register and record customer information
3. Offer spare parts
4. Provide with necessary technical support for new application
5. Visit customer regularly and correct information
Why choose us:
1. Lower investment cost for a high quality and durable machine;
2. Low energy consumption with high production output;
3. Overseas installation and training are available;
4. Machine warranty with spares in stocking and in-time delivery;
5. Fast machine delivery and installation: KWELL produces on an average of 10 sets of plastic machines per month and can deliver the machine faster than most manufacturers. The regular delivery time of an KWELL recycling machine is 30 days.
Please convenient yourselves by me !!
http://kwellgroup.en.made-in-china.com/