Multi-Disc Screw Press:
The unique design of the structure allows self-cleaning during the dehydration process, which effectively prevent clogging and save flushing water cost.
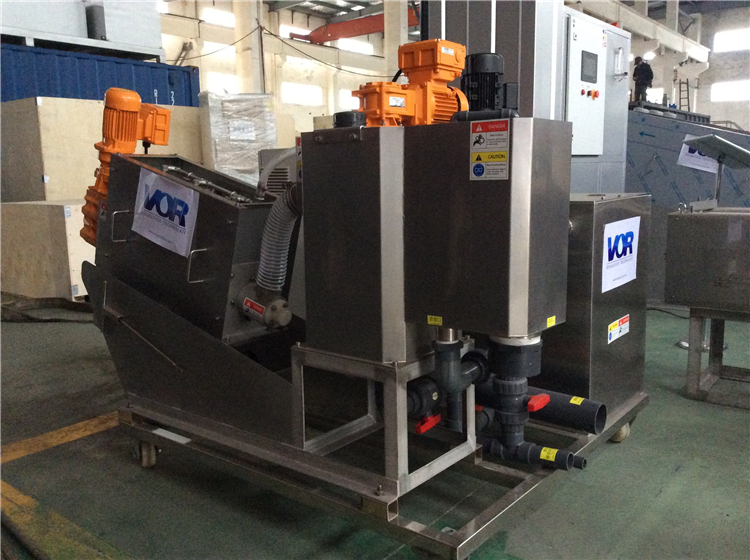
Description:
The main unit of the Multi-disc Screw Press (LS-MD) is a very simple, slow moving mechanical devise that ring-shaped “fixed discs” and “movable discs” are alternately arranged at a certain gap around a “screw shaft”.
LS-MD series can be used in an extremely wide variety of solid-liquid separation, or dewatering applications. It has made possible the direct dewatering of low concentration oxidation ditch or waste activated sludge. The already proven superior performance is enhanced by auto self-cleaning function that enables stable and constant dewatering without continuous flushing and allows 24 hr unattended operation 7 days per week.
Flow Sheet
The sludge is fed into the Measuring Tank by a sludge transfer pump; a predetermined amount of sludge naturally flows into the Coagulant Mixing Tank, the excess volume returning to the sludge tank via the overflow pipe.
Polymer and sludge are thoroughly mixed in Coagulant Mixing Tank, from there, the flocculated sludge moves into
Predewatering Zone and dewatered at Dewatering Zone in the subsequent stage by decreasing pitch distance as well as inner space. Additionally, the End Plate will further improve the sludge cake dryness.
Features
Wide application
Can be widely used in municipal sewage, food processing slurry, slaughtering and breeding wastes, printing and dyeing sludge, paper mill, tanneries, pharmaceutical, and other industrial slurries.
This equipment is an optimum choice for treating sludge that contains high oil content, such as DAF froth which filter cloth systems and centrifugal decanter cannot readily handle. What’s more, the equipment boasts a higher solid capture rate.
Capable of treating low concentration sludge
The dehydrator has both a predewatering unit and compression dehydration unit, and therefore can cope with a wide sludge concentration range of 0.5 to 5%.
Fully automatic operation
Due to the unique design, the operators can begin automatic operations of the dehydrator and related accessories by simply and easily operating the included control panel. It allows 24 hr unattended operation 7 days per week.
Clog- free and Continuous operation
The filtration surface consists of a multiplicity of discs, additionally due to left and right rotation of the moving discs, foreign substances in the gap can be permanently removed, therefore it seldom clogs and the equipment can run continuously.
Low operation cost due to the small amount of flush water and low maintenance
Continuously flushing is not needed in order to restore the original filtration performance. Only showering with a minor amount of water is necessary to wash away sludge that oozes from the dehydration section. Thus, the amount of flush water needed is minimal.
Due to the low running speed, the average of unit power consumption is only 0.1-0.01 kw/h- kg DS (1/8 of belt press, and 1/20 of centrifugal decanter), thus, greatly reduce the operation cost of sludge treatment plant.
Inhibition of secondary pollution
The equipment main unit features a semi-enclosed construction, and runs at an extremely low speed; therefore sludge does not splatter from the equipment. The dehydrator is of eco-friendly design and generated low noise and vibrations.
Compact design
The dehydrator is compact unitized construction with all of the necessary accessories and control panel mounted on a common base, and therefore can be readily installed in very limited floor space.
Customized Mobile Dehydration System
The Mobile Dehydration System offers a complete “turnkey” solution for agricultural village drainage treatment and many small scales of facilities for sludge dewatering, and carrying equipment includes:
- Multi-Disc Screw Press
- Sludge feeding pump
- Polymer make-up plant
- Polymer dosing pump
- Clean water tank (on request)
- Washing water pump
- Control panel
- Pipelines
- Odor control (on request)
- Diesel generator (on request)
Applications:
River sludge treatment
Livestock sludge concentration treatment
Oily sludge treatment
Septic tanks sludge treatment
Domestic sludge treatment
Village drainage treatment, and sludge dewatering for other small scales of facilities
Features
Compact design, simple process, mature technology, and reliable operation;
Self-cleaning, clog free, no need high pressure flushing water;
Low energy consumption, low maintenance cost;
It can cope with low sludge concentration range of 0.5 to 5%;
All equipment mounted in a standard 20GP, easy to transport.
Mobile Pilot Plants
To determine the right plant configuration as well as for sludge volume tests, VS-MD050M are available to get realistic test results.
Flowrate: 0.25 m3/hr @ D.S 5 kg/hr
Size: 1200* 850* 1035mm
Gross weight: about 180kg
Model | Raw wastewater Waste Activated Sludge Chemically Precipitated sludge | DAF sludge | Mixed Raw Sludge Aerobic Digested Sludge | ||
Sludge inlet TSS | 0.20% | 0.50% | 2% | 5% | 3% |
VS-MD-101 | ~2 kg DS/hr (~1.0 m³/hr) | ~3 kg DS/hr (~0.3 m³/hr) | ~5 kg DS/hr (~0.25m³/hr) | ~10 kg DS/hr (~0.2 m³/hr) | ~13 kg DS/hr (~0.43 m³/hr) |
VS-MD -131 | ~4 kg DS/hr (~2.0 m³/hr) | ~6 kg DS/hr (~0.6 m³/hr) | ~10 kg DS/hr (~0.5 m³/hr) | ~20 kg DS/hr (~0.4 m³/hr) | ~26 kg DS/hr (~0.87 m³/hr) |
VS-MD -132 | ~8 kg DS/hr (~4.0 m³/hr) | ~12 kg DS/hr (~1.2 m³/hr) | ~20 kg DS/hr (~1.0 m³/hr) | ~40 kg DS/hr (~0.8 m³/hr) | ~52 kg DS/hr (~1.73 m³/hr) |
VS-MD -202 | ~16 kg DS/hr (~8.0 m³/hr) | ~24 kg DS/hr (~2.4 m³/hr) | ~40 kg DS/hr (~2.0 m³/hr) | ~80 kg DS/hr (~1.6 m³/hr) | ~104 kg DS/hr (~3.47 m³/hr) |
VS-MD -301 | ~20 kg DS/hr (~10.0 m³/hr) | ~30 kg DS/hr (~3.0 m³/hr) | ~50 kg DS/hr (~2.5 m³/hr) | ~100 kg DS/hr (~2.0 m³/hr) | ~130 kg DS/hr (~4.33 m³/hr) |
VS-MD -302 | ~40 kg DS/hr (~20.0 m³/hr) | ~60 kg DS/hr (~6.0 m³/hr) | ~100 kg DS/hr (~5.0 m³/hr) | ~200 kg DS/hr (~4.0 m³/hr) | ~260 kg DS/hr (~8.67 m³/hr) |
VS-MD -303 | ~60 kg DS/hr (~30.0 m³/hr) | ~90 kg DS/hr (~9.0 m³/hr) | ~150 kg DS/hr (~7.5 m³/hr) | ~300 kg DS/hr (~6.0 m³/hr) | ~390 kg DS/hr (~13.0 m³/hr) |
VS-MD -402 | ~80 kg DS/hr (~40.0 m³/hr) | ~120 kg DS/hr (~12.0 m³/hr) | ~200 kg DS/hr (~10.0 m³/hr) | ~400 kg DS/hr (~8.0 m³/hr) | ~520 kg DS/hr (~17.3 m³/hr) |
VS-MD -403 | ~120 kg DS/hr (~60.0 m³/hr) | ~180 kg DS/hr (~18.0 m³/hr) | ~300 kg DS/hr (~15.0 m³/hr) | ~600 kg DS/hr (~12.0 m³/hr) | ~780 kg DS/hr (~26.0 m³/hr) |
All data for reference only, and throughput may vary depending on sludge condition;
Pls consult VOR for appropriate model and size.
1. Do you supply a polymer feed system with the Separa Multi-Disc Screw Press?
Yes, we can supply not only a polymer feed system but also discharge cake conveyors and sludge feed pumps to make a complete dewatering system.
2. Can the electrical control panel be designed for an Ethernet or Scada System?
Yes, Higher-level PLC’s are available when the multi-disc screw press must be included in an Ethernet or Scada System. Operator interface terminals may also be included in the electrical control panel.
3. Are mobile dehydration systems can be customized?
Yes, the mobile dehydration system offers a complete “turnkey” solution for agricultural village drainage treatment and many small scales of facilities for sludge dewatering.
4. Do you have recommended sizing and system design information?
Yes, a complete design manual, with drawings, is available.
5. What technical service is available?
Technical service is available for installation and start-up of new equipment. Existing units can also benefit from a service visit to assist in optimizing performance. Contact us for a service proposal.
6. Does VOR offer pilot testing?
Yes, VOR can provide pilot testing at your plant. Contact us for a pilot testing proposal.