Spray drying process is the widest used in the liquid forming process and in drying industry. The drying technology is most suitable for powder, particle products from materials, such as,solution, emulsion, SC and pumpable paste states material. For this reason, when the particle size and distribution of the final product, their residual water contents, the stacking density and particle shape must meet the precision standard, spray drying process is one of the most desired processes.

Principle
After filtering and heating, the air enters into air distributor on top of the Drying Equipment. The hot air enters into the drying tower spiral form and uniformly. By .passing through high-speed centrifugal atomizer on top of tower, the material liquid will rotate and be sprayed into the extremely fine mist liquid beads. Through the very short time of contacting with heating air, the material can be dried into final products. The final products will be discharged continuously from the bottom of drying tower and from cyclone separator. The waste gas will be discharged from exhaust fan.

Feature
1.Drying speed is fast
2.suitable for DRYING heat-sensitive materials
3.products with good dispersion, fluidity and solubility
4.The production procedures are simple and the operation and control are easy.
5.High drying efficiency. The liquid with the moisture contents 50-80% (for special materials, the contents may reach 90%) can be dried into the powder of particle products for one time.
6.After drying, there is no need for crushing and sieving, so as to reduce operation procedures in the production and to enhance product purity.
7.The product particle diameters, looseness and water contents can be adjusted through changing the operation condition in a certain scope.
8. SUS304 stainless steel material material
9. Control system integration operation
10.Specifically designed with a wall vibrator installed in the tower cone, so that sticky powder in the drying tower quickly fall, to avoid the product for a long time to stay at high temperatures, affecting product quality
11.The unit is equipped with quick cleaning holes in many places, easy to clean. Apply to the requirements of replacement varieties.
Special design
1. specially designed for hot air distributor, the wind is reasonable divided.
2. it is made according to the EU standard to improve the surface finish of the inner wall so that the material is difficult to adsorb.
3. the equipment is specially designed in the process of making, and it is convenient for the user to do antistatic treatment.
4. design an air hammer in the proper position of the tower body. regularly strikes the wall of the tower to reduce absorption.
Shrink the cone angle and increase the flow one cone surface.
5.Energy saving design
The main tower is designed as 3 layer structure. The insulation layer is designed between the jacket and the cover, which not only saves energy but also keep the temperature of work scene not too high. Improve the working environment, reduce the energy consumption of the factory's central air-conditioning.
6.Health design
Because the clearance needs in chemical production, especially for changing varieties The cleaning port is designed on the tower and the thicker pipeline, and the hand hole is designed for the easy aggregate part. The connection of each pipe is favorable for disassembly and installation. The whole silicone pad is used for cleaning and replacement.
The feed pipe is made of stainless steel pipe.
The material contact pipe is made of stainless steel pipe.
7.Recycling design
The wet dust remover is used in the tail gas treatment, especially designe demister to reduce the loss of water in the process of dust removal, you can use purified water as the circulating water if it is necessary to further reduce the cost of the product, the material return to the concentration process when it is set to a certain concentration, almost no loss of material.

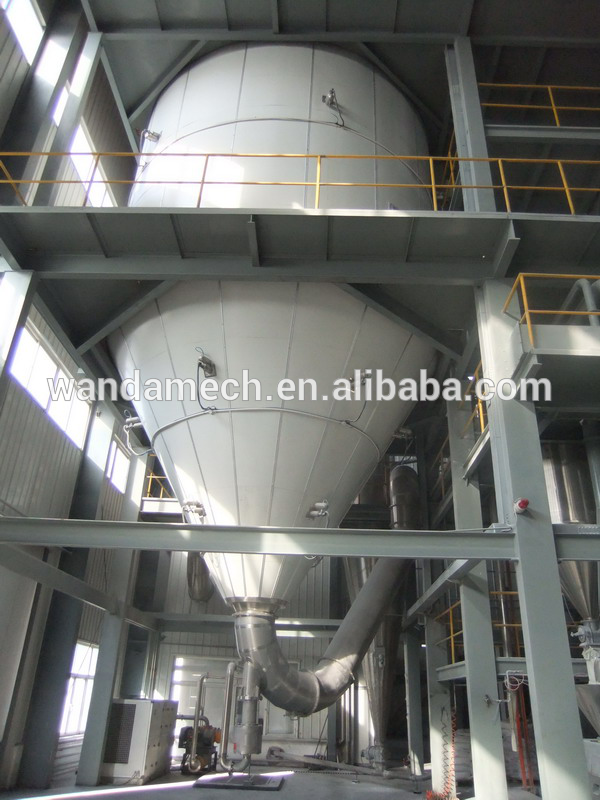
1.Schematic diagram of centrifugal dryer. Surface abrasion resistance and friction resistance.
2.Welding technology
The inner surface of the equipment should be clean, smooth and easy to clean.
The welding part of the equipment is full welding.
Acid cleaning, polishing treatment after welding
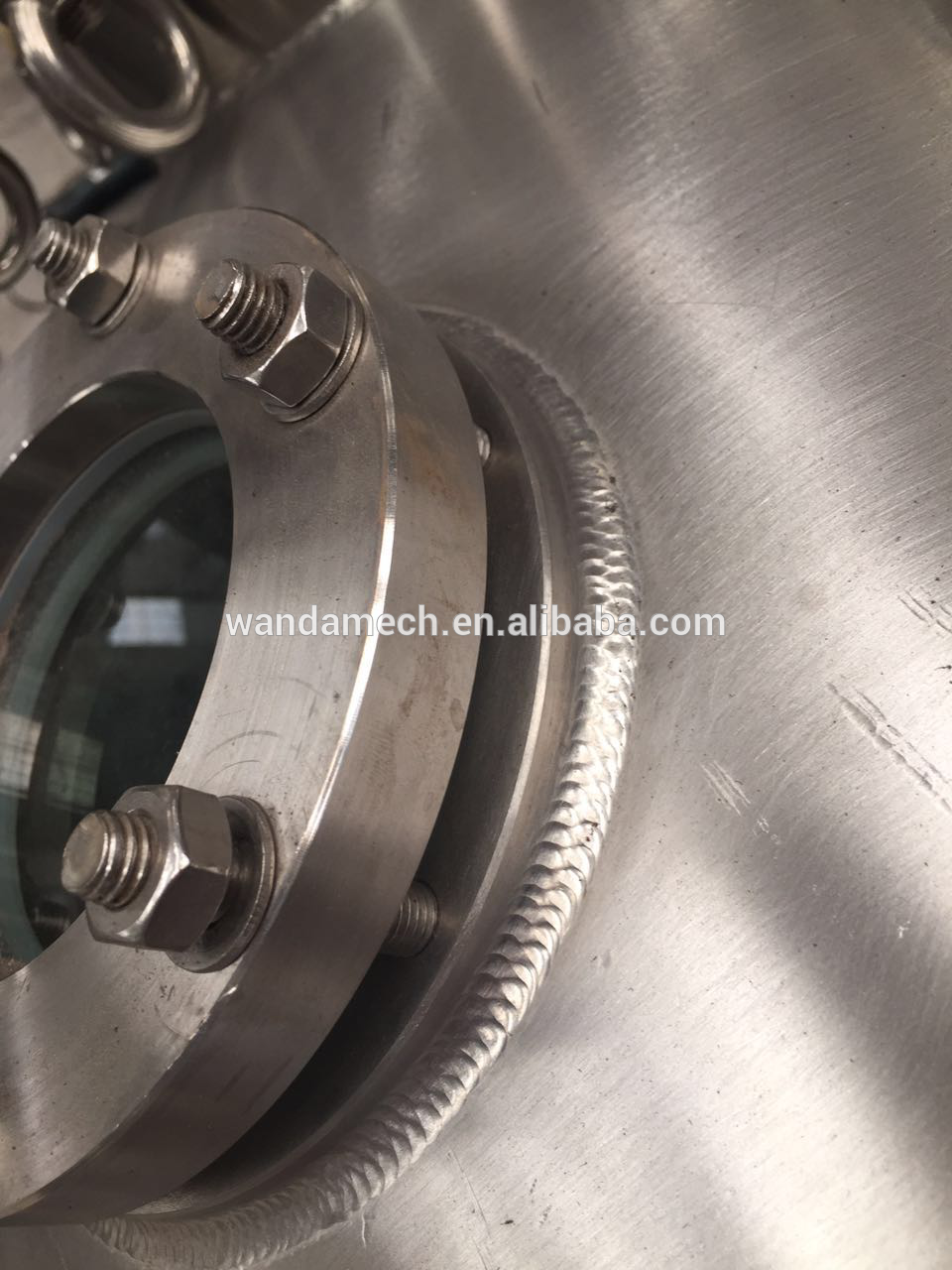

Outer surface is smooth, no concave and convex, no scratches.
4 Hot air distributor
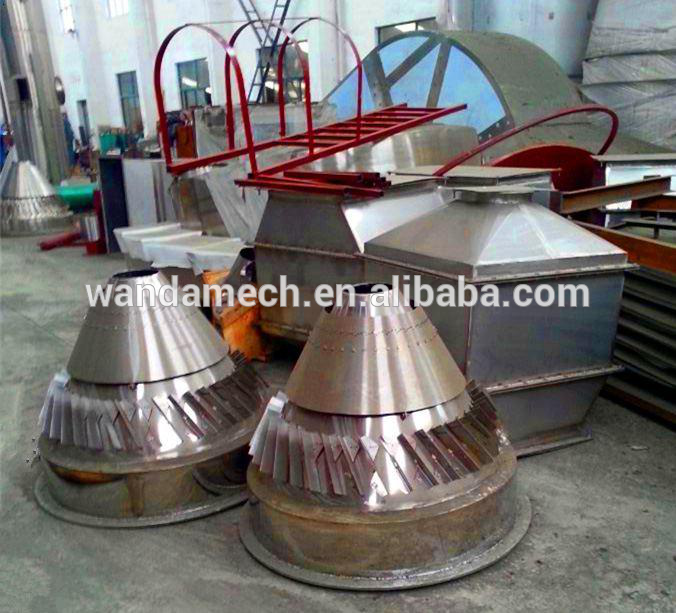
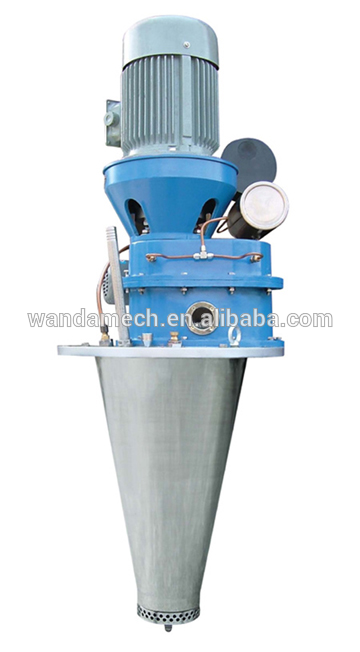
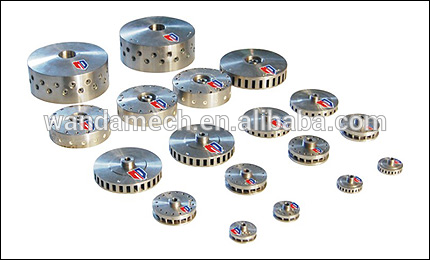
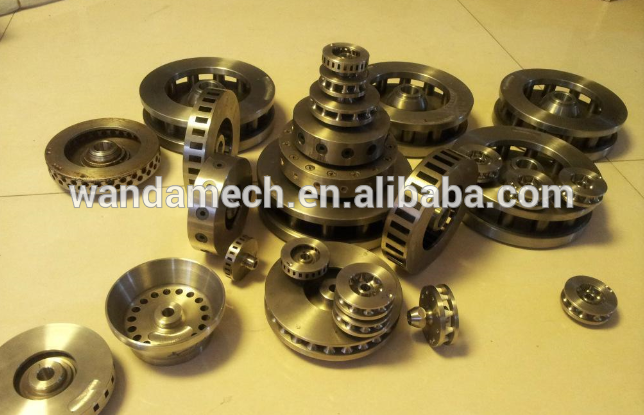
5.Atomization system(optional)
Advantage:Low failure rate, stable performance
disadvantage:Improper use will leak oil and affect the material.
Electric atomizer(optional)
disvantages: it is applicable to materials with high cleanliness requirements, small size of equipment
Disadvantages: improper use of the bearing part can be damaged, and the damage needs to be returned to the factory for maintenance.
6.Dust removal system
Cyclone separator (optional)
Advantage:small floor area, low cost, suitable for larger, granule materials
Disadvantage:Dust removal efficiency90-95%

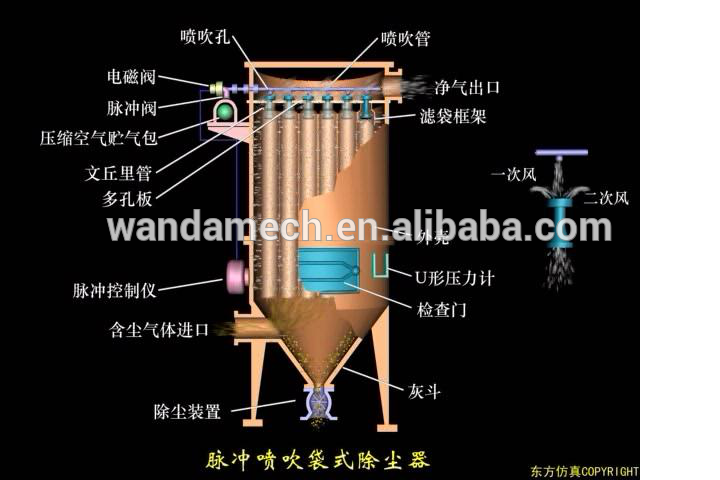
6.Dust removal system
Cloth bag filter (optional)
Advantages: 99% of dust removal efficiency, suitable for materials with light weight and small particle size
Disadvantages: large area and high cost
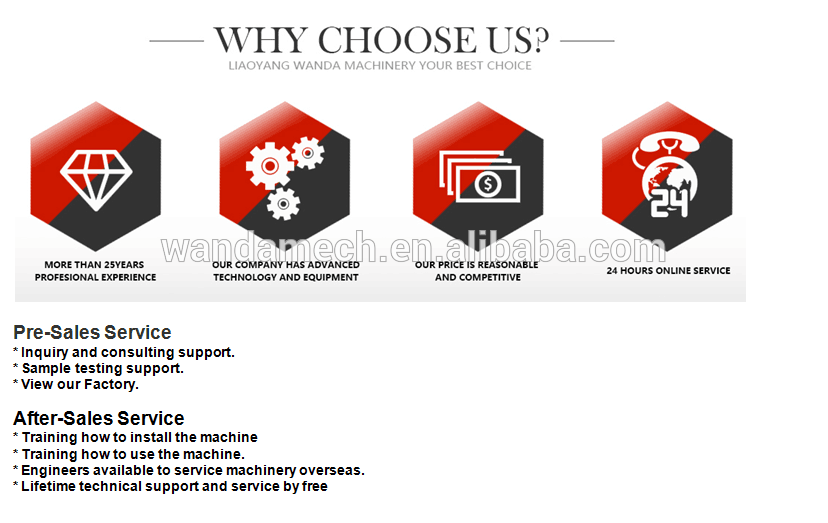

LIAOYANG WANDA MACHINERY CO.,LTD is specialized in design, development, manufacture and sale of pharmaceutical, chemical and packaging machinery.Our products include filter, centrifuge, mixer, tablet press machine, granulator, dryer, packing machine, teabag packing machine, etc. Looking to the future with a commitment to design innovation and quality products, supported by an outstanding level of customer service. The unexcelled quality medical machinery can be easily obtained from us because we maintain the quality and standard of our products from incoming raw materials to the finished products. Our Team is full of experienced and qualified professionals, who have sound knowledge about the quality of our medical machinery. Our products are far sold to Europe, U.S.A., and the southeast Asia. They are well received by customers both at home and abroad.
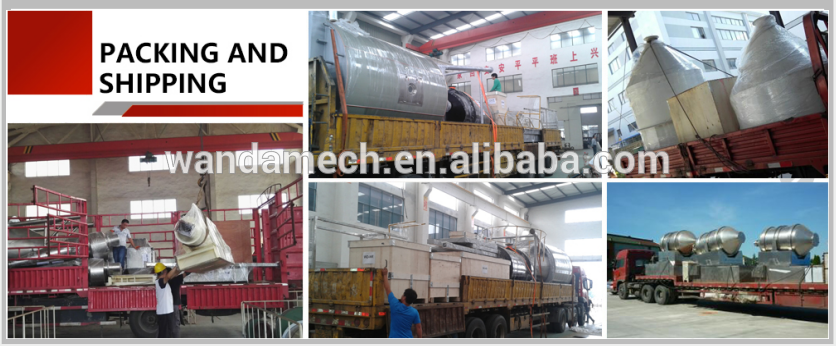
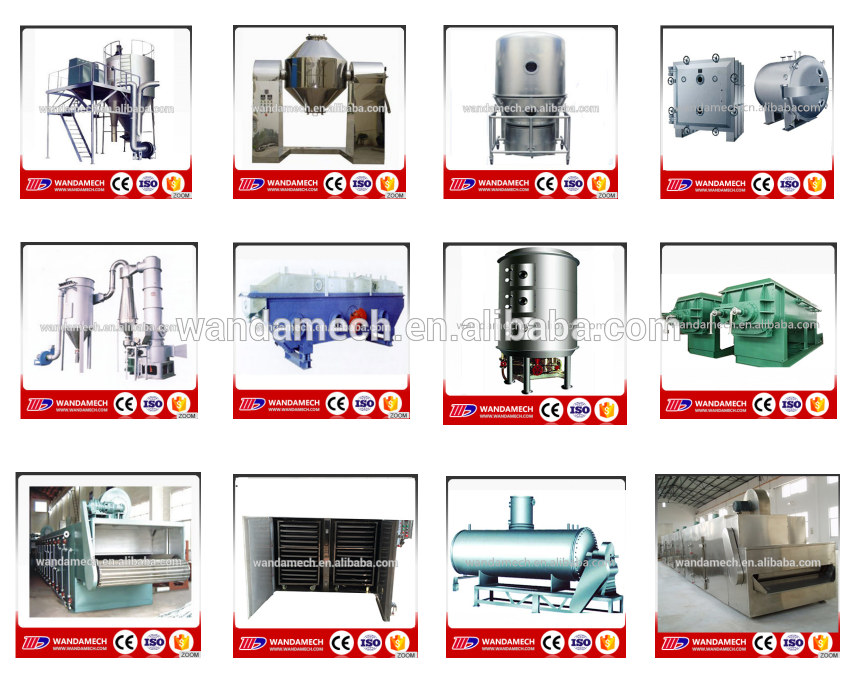
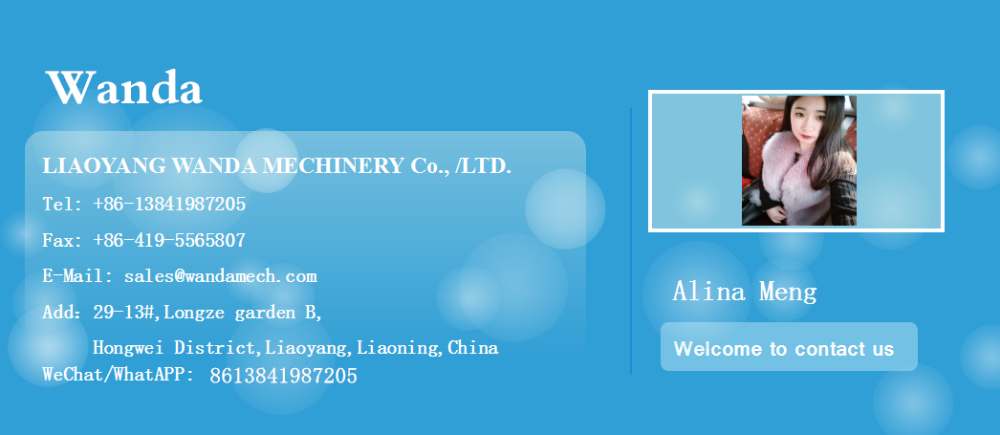