Advanced technology large economic scale Sweet potato starch production line.
Capacity: 0.5-20 ton per hour Potato starch output
Our production line:
1. Advanced and reliable Processing technology.
2. Energy-saving, water-saving, labor-saving and little pollution. hot recycling close type production and the process water will be recycled .
3.Mostly machinery with fully stainless steel to be sure these is no corrosion.
4. Advanced surface treatment craft. Oil and dirty resisting.
5. Many various capacity option.
Process description
1 Potato receiving, transporting and cleaning unit
Store the potato in storage pool. Then the de-stone machine will remove the dirt and other foreign matters completely. Finally, store the clean potato in a temporary storage hopper.
2 Potato rasping unit
The rasping unit is the most important part of potato starch extraction. Rasping mill with high efficiency allows the starch granules in the potato cells to be released out completely, which ensures minimum quantity of the remaining starch in the potato residue. The rasping potato slurry is pumped into de-sanding unit by a fiber pump.
3 De-sanding unit
Rasping potato slurry is pumped through the fiber pump into the de-sanding cyclone. When the slurry enters de-sanding cyclone, the light phase of starch and potato residue come out of the top as overflow, and the heavy phase like sands will be discharged from the bottom.
4 Starch extracting unit
Centrifugal extraction is another key unit which influences the potato starch yields. The potato slurry enters the first stage centrifugal sieve from de-sanding cyclone, the slurry is separated into starch slurry and potato residue under the centrifugal force. Starch slurry is pumped through the de-foaming pump to the hydro-cyclone station for washing starch, and the potato residue is sent to second and third grade centrifugal sieves through fiber pump for starch recovery.
5 Potato residue dewatering
We use a centrifugal sieve for potato residue dewatering, it works like the extraction sieve. Finally, potato residue is transported out of the workshop, the extracted water return to the process water system.
6 Starch washing and concentration unit
The 16 grade hydro-cyclone station guarantees the quality of the starch completely, which is the most important unit of the entire production line. The starch slurry enters the third stage of the hydro-cyclone for concentration, and the fresh water enters the hydro-cyclone from the other end which washes starch. The overflow enters two grade recovery station to recycle starch, the bottom flow is washed through 13 grade washing cyclone to ensure that the starch slurry does not contain impurities and final starch will be in accordance with national standard .
7 Starch dewatering unit
The starch out of the cyclone station has big moisture so it must be dewatered then dried. The starch slurry enters vacuum dewatering filter tank from the starch milk buffer tank. Under the vacuum formed by the vacuum pump, the starch slurry is sucked to the drum surface, then filtrate goes through filter mesh and enters the filtrate separating tank. The starch cake remains on mesh surface and is scraped off by a scraper and transported by the conveyor belt into the air dryer. Then weighing and packing.
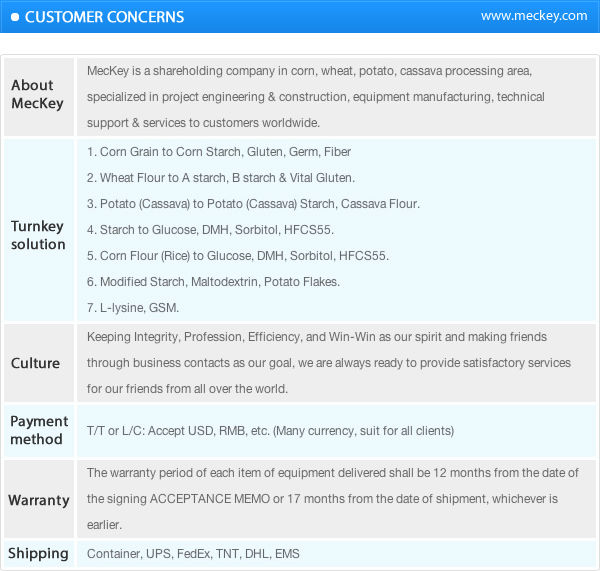
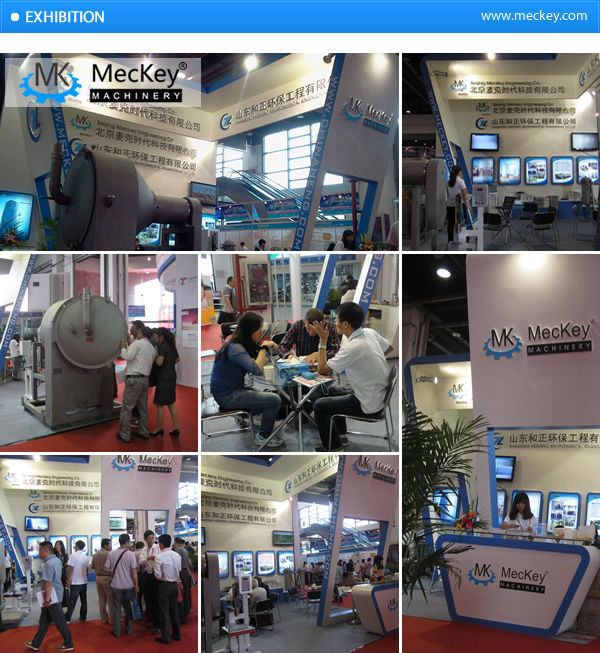
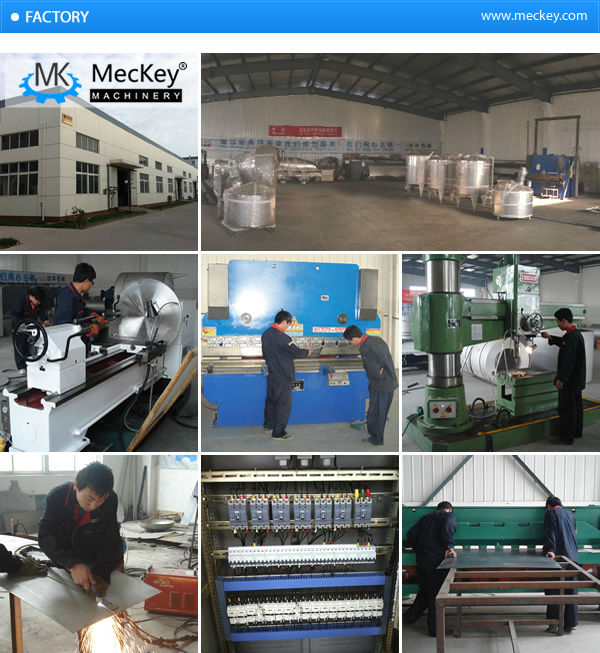
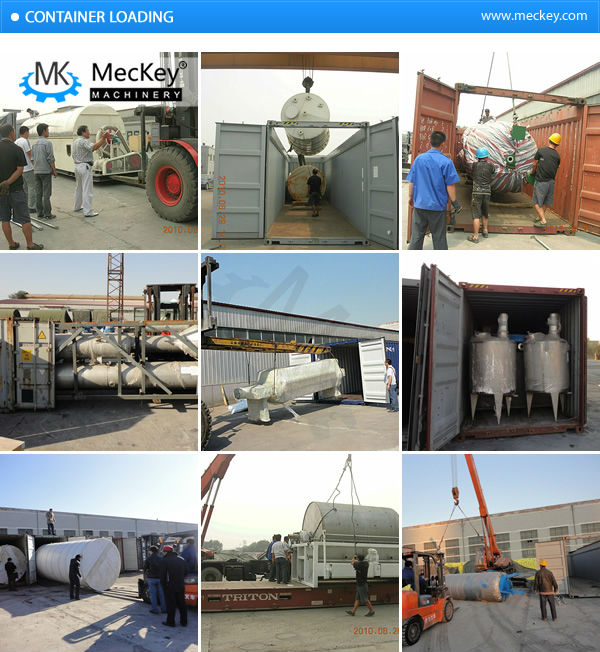
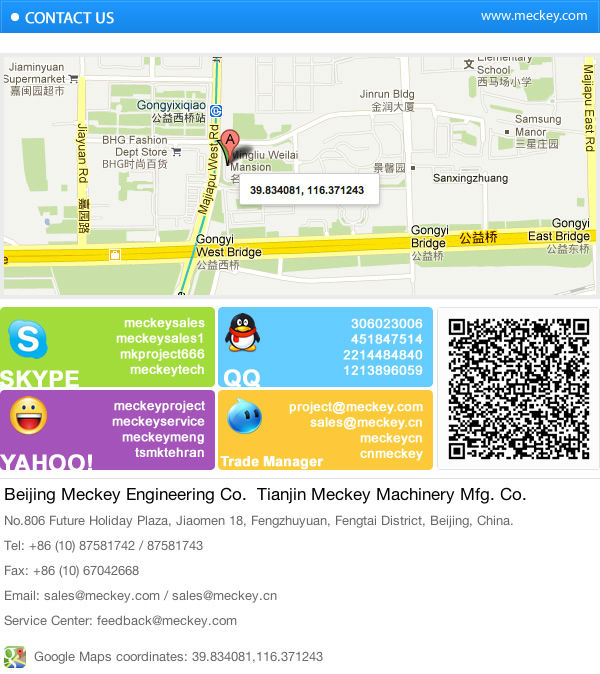