Corn Starch Syrup Production Plant,
Corn Starch Syrup Production Plant!!!
Corn glucose is widely used in many fields, like food, medicine, paper, etc.. Traditional method is processing starch to glucose, in consideration of high cost of starch, more and more people turn to process glucose from corn or rice. We adopt the newest double-enzyme method to process broken rice, the product is clear and of high quality, customers can also get protein dreg for animal feed.
Our machines are durable and performing well, the projects we finished abroad all go well and have made profits for years.
Rice glucose project - Egypt.
Corn Starch Sugar - Iran.
An corn flour glucose production line is under construction in Zambia, pls visit our website to see more about our company news: www.meckey.com
Corn glucose syrup from Iran customer recently. Clear like water!!
FLOW DIAGRAM
PRODUCT SPE.
Appearance | Clear viscous liquid |
Color | Colorness |
Dry solid | 75%,80%,82%,84% |
DE Value | 38—60 |
PH Value | 4.6—6.0 |
Coliform Bacteria(mpn/100g) | 30 (max) |
Sulfate Ash(mg/kg) | 0.5 (max) |
Salmonella | Not detected |
AS(ppm) | 0.5 (max) |
PB(ppm) | 0.5 (max) |
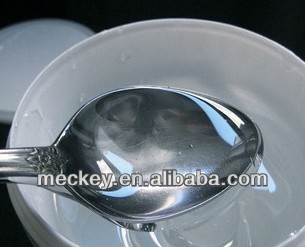
DESCRIPTION
(1) Purifying: Before going to storage bin, pre-purifying is done to eliminate big and small foreign substance which will be sent to germ cake collection section. There is a device near storage bin, it has clean, de-stone, de-dust functions. Purified corn is sent to degerm section.
(2)Peeling, rasping: the corn will be peel the skin at first, then send to the mill and broken.
(3) Milling: the broken corn will be de-germed. Then to mill and get flour.
(1) Corn flour heating: Corn flour is unloaded to the feed chute. With water adding, it is sent to the heating tank for softening. The heated corn flour milk is pumped to the ejection section.
(2) Liquefaction:flour milk is sent to buffer tank then liquefied by jet cooker with the aid of enzyme. 2 times jet cooking is needed for better reaction. Then the material is sent to flash for cooling then to the neutralization tank for suitable PH value.
(3) Dreg separation and drying: The liquefied material goes to filter press for separating the dregs. This dreg can be washed via process water to recover the liquefied liquid. Then it is sent to bundle dryer for dreg drying.
(4) Saccharification:The liquefied material is sent to saccharification tank for reaction with aid of enzyme. After being kept in holding tube the required DE value of the glucose will be reached. Then the material is sent to flash for cooling then to the enzyme killer to kill the enzyme.
(5) Filtration and decoloring: Glucose is cleaned by removing the protein and other foreign items with filter. Active carbon is needed for decoloring at proper temperature. After decoloring, the AC will be removed by filter. And then the material will be sent to the next section.
(6) Ion exchange: Tiny foreign items and bad odor is removed via ion exchanger. This equipment is used for high quality product.
(7) Evaporation: The glucose is totally cleaned through safety filter then sent to evaporator for concentrating to reach the required DS as final product.
1. Q: If I want to know the price, what info should I provide?
A: You should inform us some basic info , such as: raw material, final product, input capacity or output capacity, specifiction of material and product, etc.
2. Q: If I already have a production line, can I add some machines to increase the capacity?
A: That's viable, pls contact us and we can help you find a suitable solution.
3. Q: How about the automatic level?
A: Depens on you, we have manual/ semi-automatic/ full-automatic control.
4. Q: How about the installation and commissioning?
A: We can send our engineers abroad for the supervision.
5. Q: What's the capacity you can supply of the project?
A: 10000tons per year to Max.
6. Q:What's the brand of your equipments?
A: Most of them are made in China with high-quality.
Sea Worthy Package and according to the customer's requirement.
3-4 months after getting the downpayment.
1) Implementations of automation systems, computer 2D/3D modeling and advanced
CAD/CAM technology.
2) Turn-key plants for the production of wheat starch, corn starch, potato starch and
starch derivatives such as glucose, fructose, crystallized glucose, sorbitol,
etc.
3) Professional engineers with ample on-the-job training experience.
4) A team working at site for the guidance of installing, commission works.
5) Low water and low energy consumption design to save your money.
6) Equipments are made of stainless steel, one year warranty, life-long maintenance.
C-Credit: We promise only what we can do to do our customers and keep our promise.
E-Efficient: Our work is efficient based on our qualified staff and company’s standard working
process.
E-Exact: We study your requirements and supply exact solutions to you.
S-Standard: We have standard systems to guarantee our activities to be complied with
international ones.
WE ARE WHERE YOU ARE
By choosing MecKey you are choosing the perfect long-term parter for your daily operation. Our
service network can reach you wherever you are.