Pre-sale service: Provide customers the parameters and confirm technical points Share photos and videos With clients Show our factory to clients for checking |
On-purchase service: Keep clients informed Of the production progress Send photos to clients before shipment for checking Arrange the visa for engineers who will go for guide assembly |
After-sale service: Training and all-around technical guidance for operation commission and maintenance Engineers abroad to for guide assembly Detailed drawings from front view, vertical view ,side view. |
TONGFU Factory Introduction:
Liyang Tongfu Machinery Co.,Ltd is a large-scale new energy equipment manufacturers in China.
Our main products are pellet mill for energy industry, feed-stuff industry and we are dealing with Construction Waste Crushing and Recycling Work station.
1.)Years of experience in pellet machine production field.
2.)Approved ISO9001 and international certificate: CE and SGS.
3.)factory audited by SGS.
4.)Over 100 stuff and 50,000sm factory occupation.
5.)Specialized in designing, researching, developing, manufacturing and exporting.
6.)Exported to over 20 countries and finished more than 100 turn-key projects.
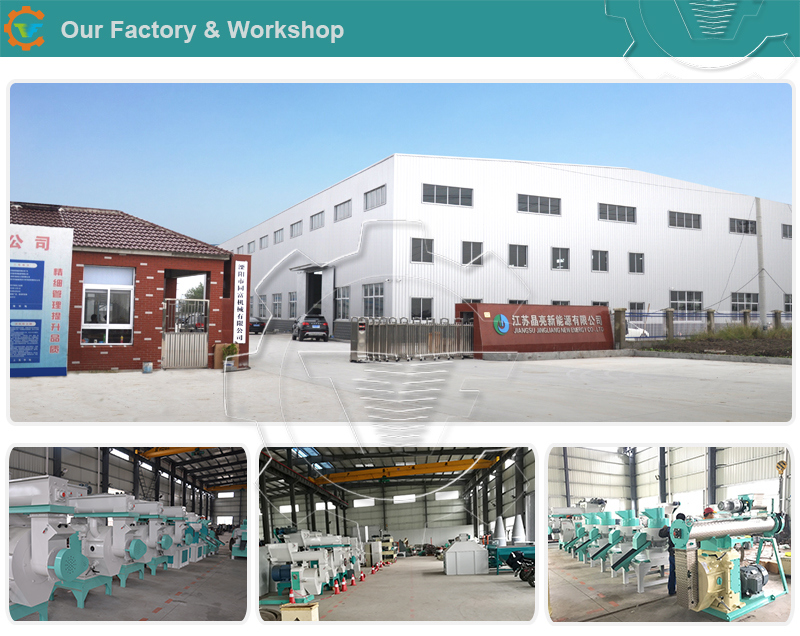
Features of Pellet Feed Plant
The feed pellet production line is manufactured to produce feed pellets. The machines can be match different size of ring die hole size , such as φ1.0,φ1.2,φ1.5,φ2.0,φ2.5,φ3.0,φ3.5,φ4.0,φ4.5,φ5.0,φ6.0,φ8.0 , always for making shrimp, fish feed to use for φ1.0--3.5 ring die ; chicken feed for φ3.0; Swine feed for φ3.0--4.5; Cattle, horse for φ6.0--8.0).
CE large scale cattle pellet feed production line |
Feed Pellets Processing Technology Raw Material → Feed Grinding → Feed Mixing → Feed Pelletizing → Pellet Cooling → Pellet Crushing → Screening & Grading → Pellet Packing |
Equipment Related to Complete animal food production plant Feed Grinder →Feed Mixer → Feed Pellet Mill → Counter flow Cooler → Feed Pellets Crumbler → Feed Pellets Grading Sieve → Weighing and Packing Machine |
Raw Material corn, maize, grass, grain, SBM, MBM, alfalfa, molasses, straw.etc |
Output livestock feed pellets, poultry feed pellets, aquatic feed pellets, etc. |
Capacity 1-50TPH |
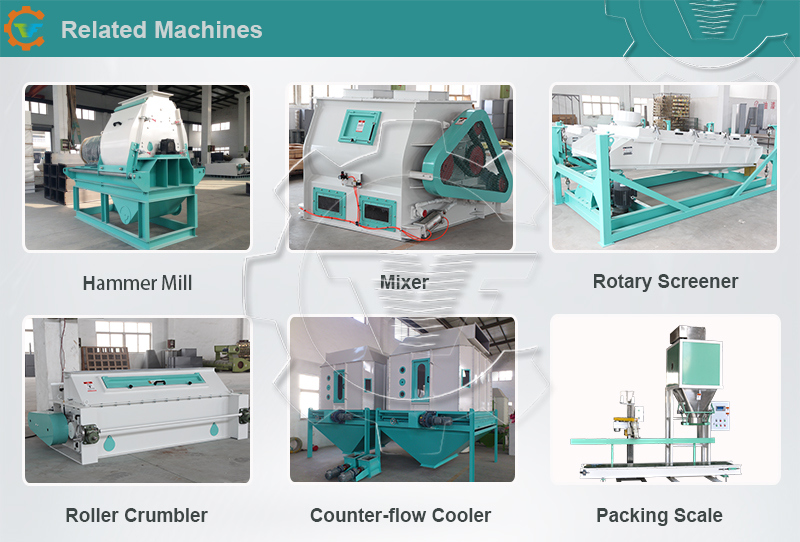
Detail Description of Pellet Feed Plant
1.Raw Materials Receiving &Pre-cleaning System of Complete Feed Mill Plant
All the solid ingredients packed in bags for feed production would be received in plant by road.
Their materials will be store in store godown. According to requirement these material will be
dumped manually in dumping hopper and conveyed to the pre-cleaner through the mechanical
conveyor system.
2. Crushing System of Complete Feed Mill Plant
This is a process of breaking solid ingredients to a required size. Finer the material higher will be the surface area exposure to heat and moisture to accomplish the gelatinization in conditioning. A fine
grinding material can transfer his maximum energy to the animal as compare to a course grinded
material. It is a very energy consuming process.
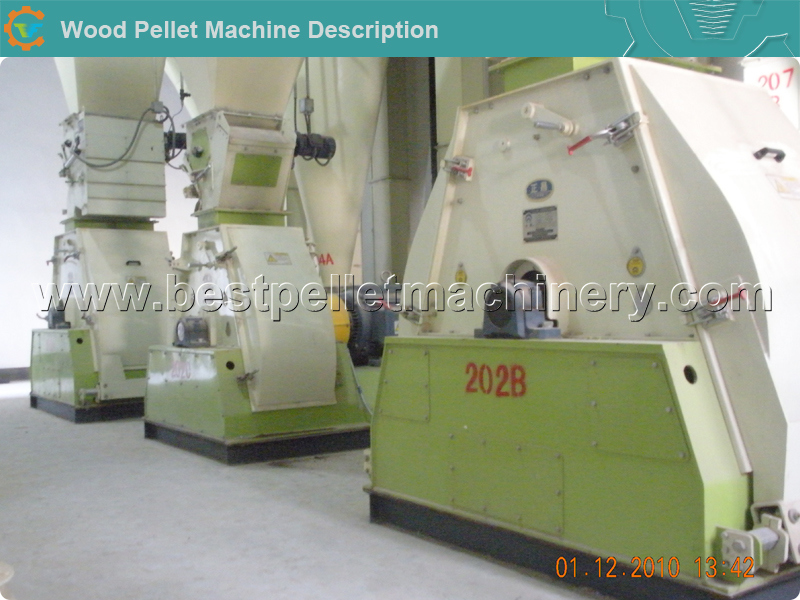
3. Mixing System of Complete Feed Mill Plant
As the name implies "Mixing" is a process of combining blending of micro ingredients. A proper mixing can be defined with a unit called co-efficient of variation. Smaller the co-efficient of variation higher will be the quality of mixing. Our well designed mixer machine has such a great quality. Beyond this is a mixer machine should have a provision to mix liquid to it as we need oil
or molasses addition to the feed.
4. Pelletizing System of Complete Feed Mill Plant
Feed pellet machine is a main step of any pelleting plant. It is a process of converting any powder to solid shape called pallet. In this process the powder material is extruded through a well designed die with the help of rollers to convert it in to pallets. The quality & production of pallet mill depends on so many parameters.
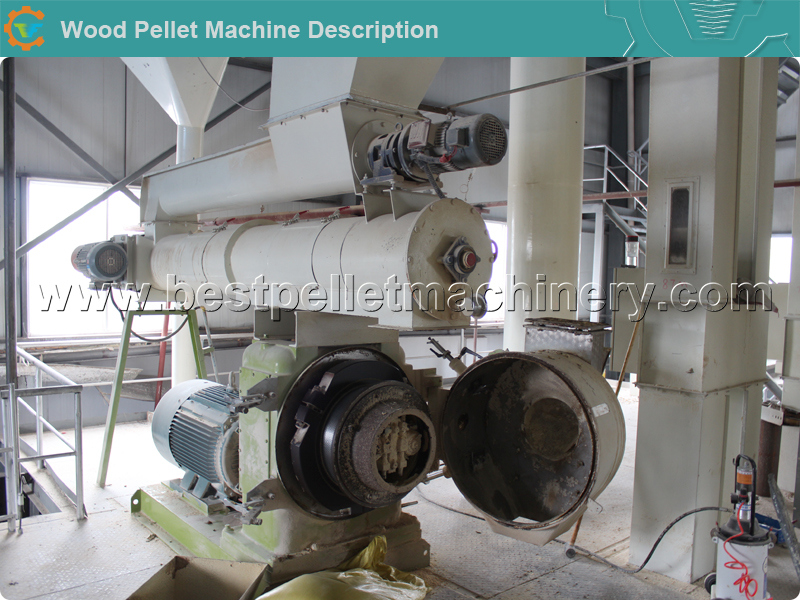
5. Cooling System of Complete Feed Mill Plant
Cooling is a process of removing heat. As we know during conditioning we add heat and moisture and also through palleting process heat generates by extrusion process. But the pallet should have a standard moisture and heat to attain its life of storage and make it safe from fungus. So we have to remove extra heat and moisture from the pallet. All this is done with the help of a well designed counter flow cooler.
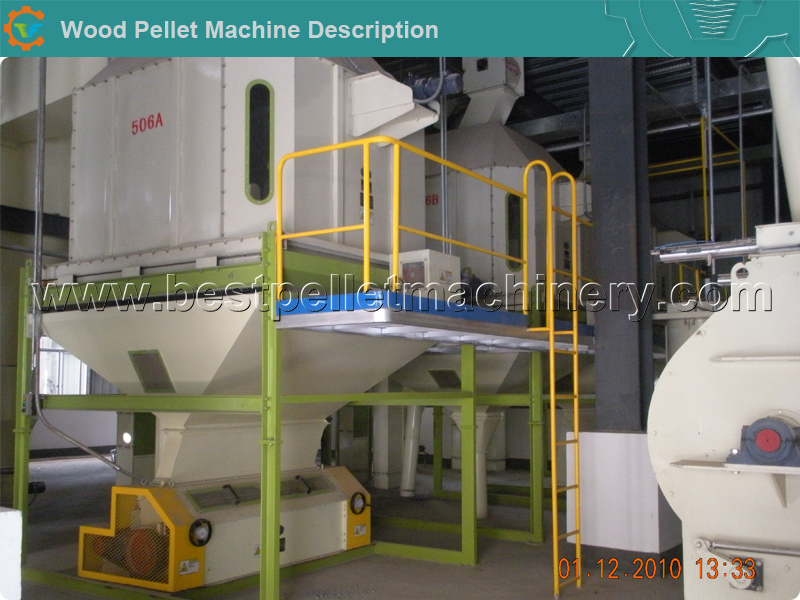
6.Crumbling System of Complete Feed Mill Plant
Crumbling is a process in which pallets after cooling is broken in to small pieces to make it suitable for small chicks or hens. When there is no need of crumbling, we by-pass the feed directly to the screen with the help of By-pass Mechanism. A well designed crumbier should have capability to break the pellets without making much finer.
7.Rotary Screener System of Complete Feed Mill Plant
Pellets are conveyed through a sieve to remove impurity and deformed pellets. Fines and deformed pellets are recycled back to bins before the pellet mill. Sieved pellet with different sizes are stored in individual bins.
8.Packing System of Complete Feed Mill Plant
The end of process in every plant is bagging also called packing. After screening the finished products are filled in to bags. In small and medium plants, bagging can be carried out manually but for higher production it is batter to go for electronic bagging machine.
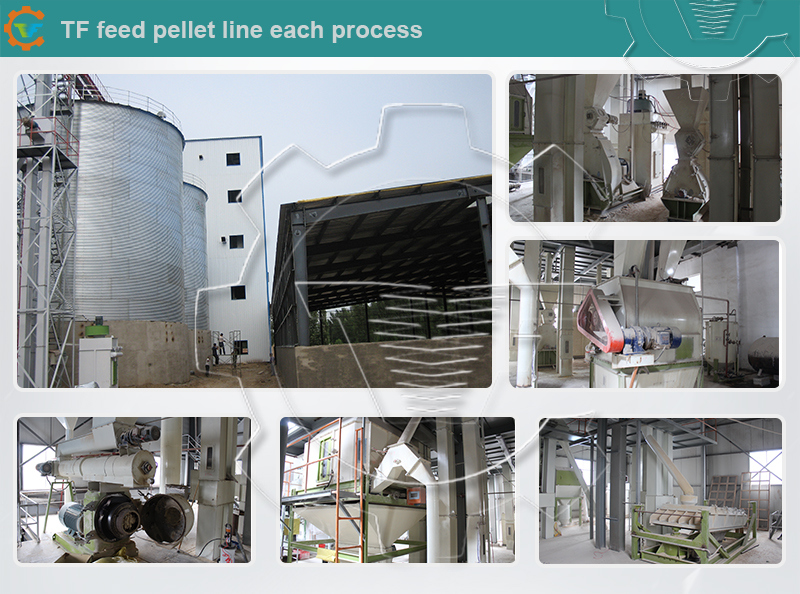
To get best solution, please tell us:
1) What kind of animal that you produce feed for?
2) What are your main raw material?
3) what about the capacity you want to get? (how many ton per hour or day or year)
FAQ
1) Could the feed pellet mill plant be used for different kinds of animal and poultry?
Yes. of course.
What we need to do is just have different size of ring die mould according to the requirement of different animal and poultry. and the replacement of the ring die mould is very easy. It could produce feed for chicken, pig, cow, cattle, goat, rabbit and fish, etc.
2) What kind of raw material that the conditioner and the ring die mould are made of?
Both of the conditioner and ring die mould in our macine are made of stainless steel. should to note that there are some suppliers in the market adopt carbon steel. please pay more attention on this point, lest the unexpected trouble.
3) What is the suitable moisture (water content) of the raw material that easy to make feed pellet?
The ideal raw material moisture range is from 15% to 18% .
Please contact us freely for detailed information!
www.bestpelletmachinery.com